Webinar Replay | Sign up now for our latest webinar replay: "Tackling Supply Chain Disruptions: Michelin’s Approach to Resilient"
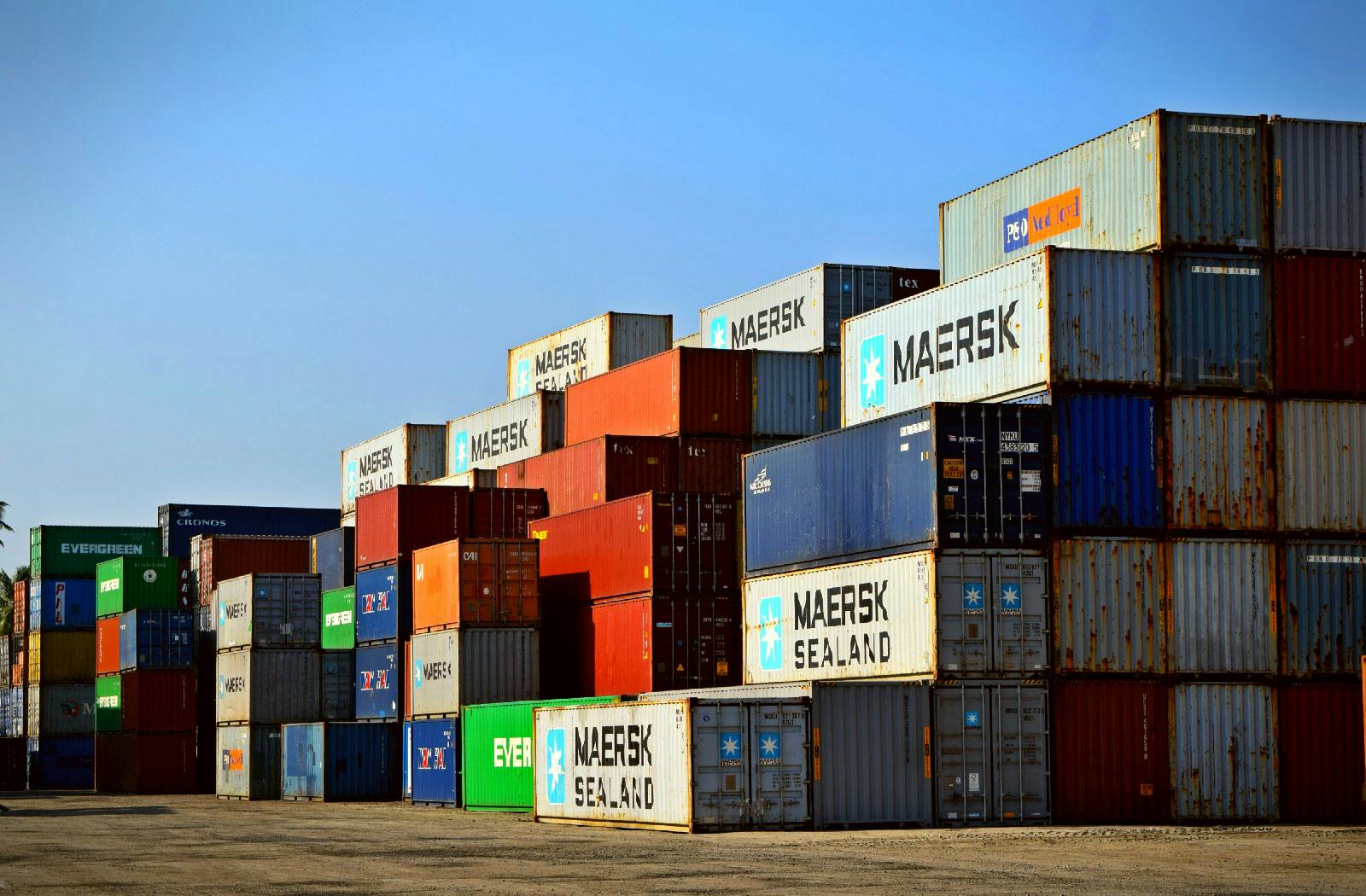
How to capitalize on carriers’ new storage offer to face Covid-19 situation
The current COVID-19 pandemic has set off unprecedented upheavals that bring out major challenges on supply chains and transport operations across the world. Carriers are adjusting their offer by creating new storage services to help their customers to overcome these challenges.
New storage services limit the impact of the current Coronavirus crisis on supply chain costs and enable customers to be more reactive
As of today, CMA CGM launched a “Delay in Transit” solution to temporarily store containers in dedicated transshipment hubs. MSC also initiated its “Suspension of Transit” program at six transit hubs offering storage on staging sites near ports of call and storage at origin for companies looking to slow down their supply chains.
These new services are designed to limit costs for customers who face high warehousing storage costs at the destination, demurrage, per-diem, and other charges. Detention in dedicated hubs will also limit excess inventory in factories and warehouses.
Containers shipped before the European lockdown from Asia are now starting to land at major ports in Europe. In the meantime, retailers and manufacturers fail to pick up containers because warehouses are full or closed as demand has plummeted. As a result, European ports and warehouses will face a logjam of manufactured goods in the coming weeks. These services will help to slow inbound container flows from Asia and limit congestion.
This detention in transit service will also speed up time to market once operations resume at the destination. As such services provide customers with container yard storage at main transshipment hubs worldwide, it ensures that goods can be available at the destination as soon as possible by bringing cargo closer to markets and alleviating the risk of congestion or shutdown at ports of unloading.
Keep track on in-transit stock is key to make supply chains more resilient in this changing situation
Monitoring the stock of containers in locations out of the standard transportation plan is complicated. Detention in transit is not a standard service in the industry. Logistic teams need to consolidate many data from different providers to evaluate where the stock is located, to which PO it is related, for which final destination and client, etc. To provide such information, logistics teams need to perform time-consuming manual or semi-manual operations, leading to uncertain data. Keeping track of these containers is a real brainteaser.
By centralizing all data from carriers and freight forwarders and direct information from the transshipment terminals on a unique platform, Wakeo removes the operational complexity while providing an efficient and reliable tracking tool based on real-time information. Details such as PO numbers, SKU, client, etc. can be easily gathered thanks to a unique tracking intelligence, making it easier to locate stocks even if they are scattered in numerous transshipment ports or hubs.
Optimizing supply chain efficiency and agility is challenging in the current COVID-19 situation. Having real-time visibility of the in-transit stock is key to adapt quickly to market trends and take reactive actions based on reliable information.