Webinar Replay | Sign up now for our latest webinar replay: "Tackling Supply Chain Disruptions: Michelin’s Approach to Resilient"
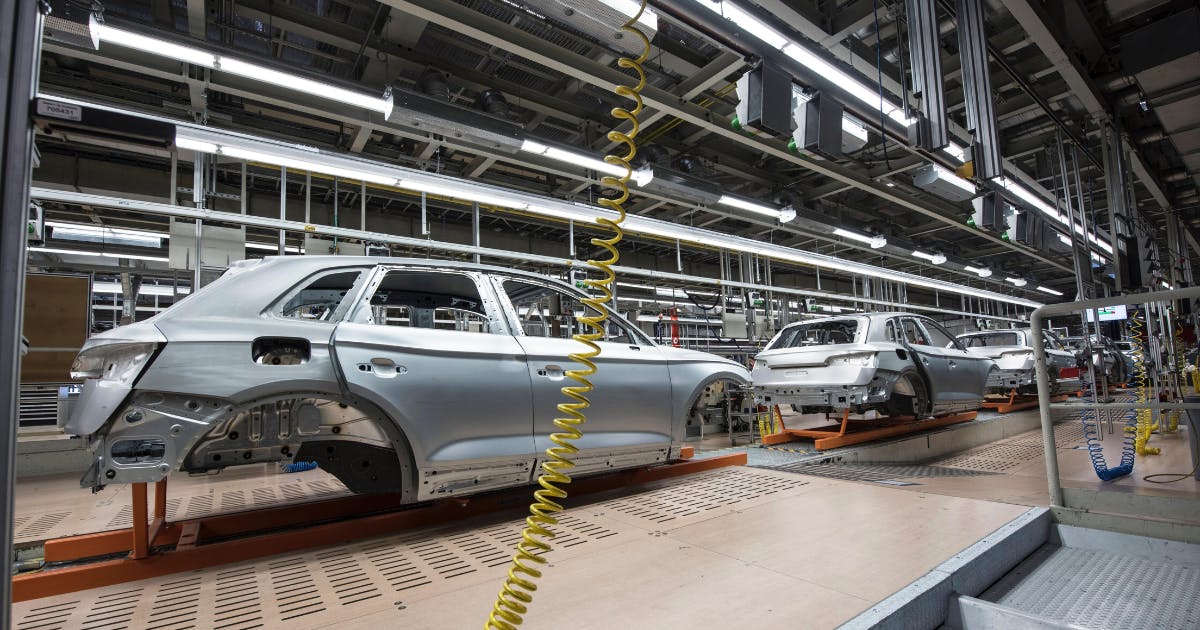
The supply chain resilience checklist for automotive industry leaders
The automotive sector has experienced a lot of instability over the past couple of years, particularly in Europe.
Challenges include a lack of components needed to digitalize vehicles and changing buying patterns, as electric vehicles gain popularity and market share. There has also been upheaval in demand and a fluctuation in the availability of logistics transport.
In a report on meretmarine.com about a recent meeting of The European Car Group (ECG), the ECG said a decline in vehicle production in 2021 - caused by difficulties in the supply of materials and semiconductors - led to a fall in demand for transportation. This was reversed in 2022 and manufacturers have since been “seeking to secure logistics capacity in a shrinking market”.
Reduced capacity has been caused by the scrapping of outdated trucks and a lack of drivers; the retiring of some older ships and the sales of some to the Asian market. In addition, obsolete trains have been taken out of service; and there has been a lack of investment. These challenges are now causing delays for many.
Speaking at the 2022 logistics summit masterclass, Wakeo’s VP of customer excellence, William Brachini warned that the cost of having to halt an automotive production line as a result of low stock can be as much as €20,000 per minute.
He also called attention to the savings to be made from reducing the need for last-minute haulage. A McKinsey report said increasing the overall utilization of transport assets and reducing the number of emergency deliveries is expected to save the industry €2 to €4 billion.
Access to quality data enables companies to better manage stock levels, pre-empt problems and make quicker, more informed decisions - all of which saves money.
Speaking at a recent masterclass, a major car manufacturer said that: “It is not just a matter of calculating lead times, of looking at where we are, but of presenting a proactive view of the supply chain to avoid disruption for our customers. For us, customer downtime costs a fortune. Wakeo can help us prevent chain stoppages and stock-outs.”
Case study success
Improved management of inventory, reduced delays and increased productivity are among the benefits achieved by the car manufacturer using the Wakeo real-time visibility transport solution.
The automotive business said that while it had initially invested in the real-time supply chain tracking tool as a “comfort solution”, the Covid crisis has led it to view it as a “necessity”. It said it has already saved the business time and money and it has plans to build on its use of the system.
Here it expands on the three key areas in which it has already noted success with the Wakeo platform:
1. Management of inventory levels
The company manages inventory levels using a dashboard that is fueled with updated data from Wakeo. This shows where all its containers are positioned and enables it to calculate an estimated time of arrival (ETA) of those shipments.
It also uses it to monitor projected stocks and anticipate shortages. It carries out projected stock simulations almost daily to define a date from which it must order by air to meet the deadline. It also tracks containers at least once a week, particularly since it has seen delivery times spike from 70 to 90 days.
“When we see that a container deviates from the standard transport time, we start to look at what's in that container and work on our projected stocks,” it said.
The business requests that suppliers use its chosen carriers, not only because it has typically negotiated better prices, but because they are mandated to send data to Wakeo, which means it can track progress.
2. Management of lead times
The company says it is beginning to take a more “preventive than curative” approach to delays.
A customized dashboard shows trends route by route, forwarder by forwarder, enabling it to see how many containers arrive on time and the average lead times per route. It uses this data to update safety stocks, which are “calculated in terms of the number of days of lead time in relation to variations in customer demand, etc.”
It says as well as using this information to update its carrier lead-time in its ERP system, it also works on the fixed horizon that it gives to the supplier, because they, in turn, need a particular timescale in which to order material and prepare shipments.
“The longer the container takes, the longer the routes, the longer the average lead time, the more we have to give firmness and visibility to the suppliers too.”
Better anticipating lead times and improving collaboration with suppliers has helped to avoid triggering the need for airfreight.
3. Management of productivity
“The third area where we see an advantage, and it’s a new field that we're developing with Wakeo, is productivity management,” said the manufacturer.
The company said in the context of inflation they have sometimes seen prices increase tenfold.
It is analyzing its use of container space to try to ensure it uses all of it where possible. “Given the price of containers, each cubic meter or each kilo costs us a fortune over long distances.”
It is in the process of setting up its dashboard to identify on which routes it experiences the biggest losses from unused space. It then plans to either offer incentives to its forwarders if they are in charge of consolidating consignments; or ask material planners to simulate the filling of the container prior to collection at its port of departure.
Next steps
In addition to having plans to further develop its use of the tracking platform, the company is planning to calculate its global carbon footprint for all transport modes.
It is increasingly important for all industries to be able to measure and control their actual global carbon footprint with reliable data.
The granularity of the information, including whether additional stops have been added and the weight of shipments, enables Wakeo’s carbon footprint calculator to provide accurate, up-to-date data at their fingertips.