Sign up now for the retail focus webinar replay and learn how to leverage data and visibility to turn the supply chain into a competitive advantage!
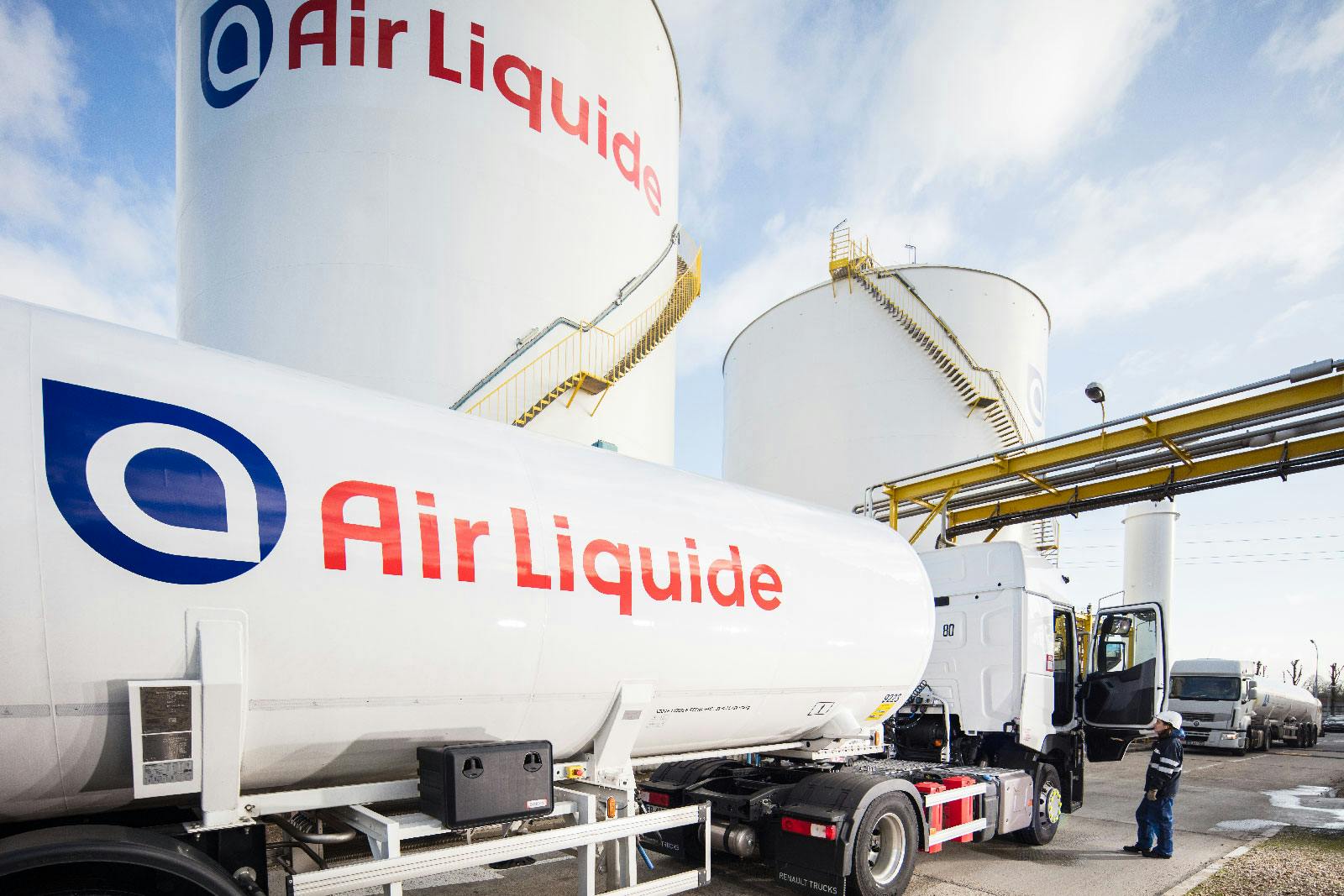
Air Liquide: from reactive to predictive supply chain with Wakeo
As a world leader in gases, technologies and services for Industry and Health, Air Liquide has more than 67,000 employees and serves more than 3.7 million customers and patients in 80 countries. Air Liquide provides oxygen, nitrogen and hydrogen which are essential small molecules for life, matter and energy.
Helium transportation requires thorough management and optimized shipping route
Within Global Markets & Technologies WBU, Air Liquide Global Helium team ships 40 feet cryogenic containers filled with liquid helium directly from its sources to its customers all around the world. Helium must be transported at -269°C in insulated containers that must be shipped within 40 days to avoid helium evaporation due to pressure rise. Helium’s supply chain is complex, as helium is a high value and sensitive material. Air Liquide equipped all its containers with IoT sensors to control and secure transportation parameters.
To cope with this race-against-the-clock, Air Liquide relies on a large panel of transport providers. As it comes from a multiplicity of forwarders and carriers’ proprietary systems, data is fragmented and heterogeneous which leads to a lack of visibility on transport flows and a lack of reliability on ETAs, even though such information is crucial to efficiently manage critical flows.
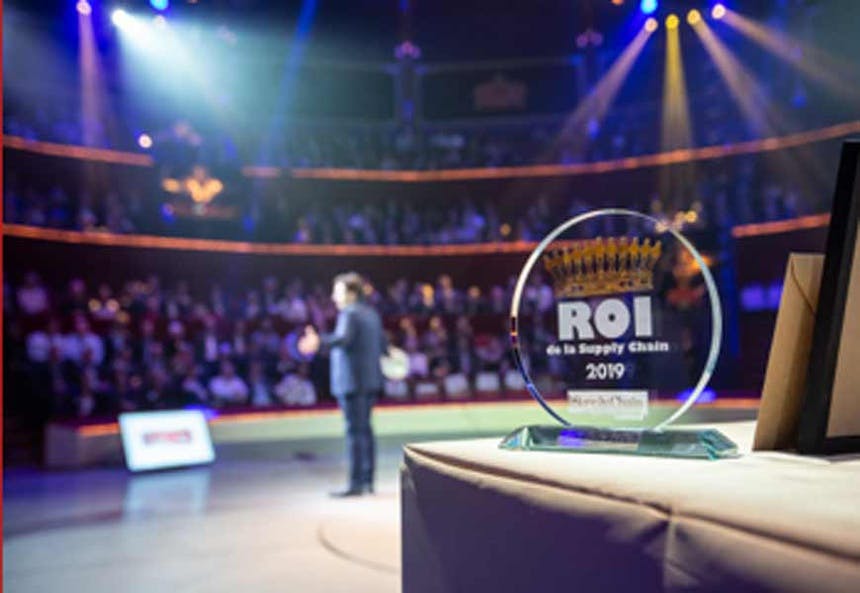
Since 2017, Wakeo works with Air Liquide teams as a strategic partner to design the best real-time tracking solution that allows them to optimize their flows and make data-driven decisions across their entire supply chain. Wakeo and Air Liquide won the renowned Les Rois de la Supply Chain innovation prize in 2019 for this strategic partnership.
Real-time tracking and data science help Air Liquide to anticipate risks
By consolidating real-time tracking data with real-time IoT information and analyzing this data through machine learning and advanced algorithms, Wakeo solution predicts transportation issues and automatically sends alerts to operational teams. Once warned about delays and pressure variations, operational teams can anticipate risks and take proactive decisions accordingly. Thanks to predictive information lead by advanced proprietary algorithms, Wakeo enables Air Liquide to have an average of 8 days of anticipation and reduce emergencies by 75%.
Optimized transport flow and reduced lead times enable Air Liquide to reduce losses and enhance capital rotation
With real-time visibility and data on pressure variations, Air Liquide teams are able to optimize transport flows and shorten lead times, reducing helium losses by 10% and in-transit inventories by 10%.
After realizing such success, Air Liquide is actively planning to expand the integration to port to facilitate the inland logistics process to reduce storage cost and enhance the containers’ rotation.
To know more about port integration, see our article on how Wakeo and Portbase team up to optimize transportation lead time.