Webinar Replay | Sign up now for our latest webinar replay: "Tackling Supply Chain Disruptions: Michelin’s Approach to Resilient"
- Sector
Oil and Gas
- Scope
20+ countries Middle East, America, Europe and Asia
- Users
100+ users including 30 from the operations teams & 70 end-users
How Air Liquide is leveraging Wakeo data to build a unique customer-centric experience
Air Liquide is a 120-year-old world leader in producing and delivering gases such as oxygen, nitrogen, hydrogen and helium, to industrial businesses and the healthcare sector. It serves more than 3.8 million customers and patients in 78 countries worldwide, supplying through direct pipelines, on-site production and via road and sea freight.
Air Liquide Global Helium teams ship 40 feet cryogenic containers filled with liquid helium directly from its sources to its customers. Helium’s supply chain is complex, as it must be transported at -269°C in high value super insulated containers. If those containers are not delivered within 40 days, helium evaporates into the atmosphere under the effect of pressure. To win this race-against-the-clock, Air Liquide relies on a large panel of transport providers and strives to always find the fastest and most reliable route to supply its customers. In this context, data can be fragmented and it becomes more and more difficult to access reliable information, even though such information is crucial to manage flows efficiently.
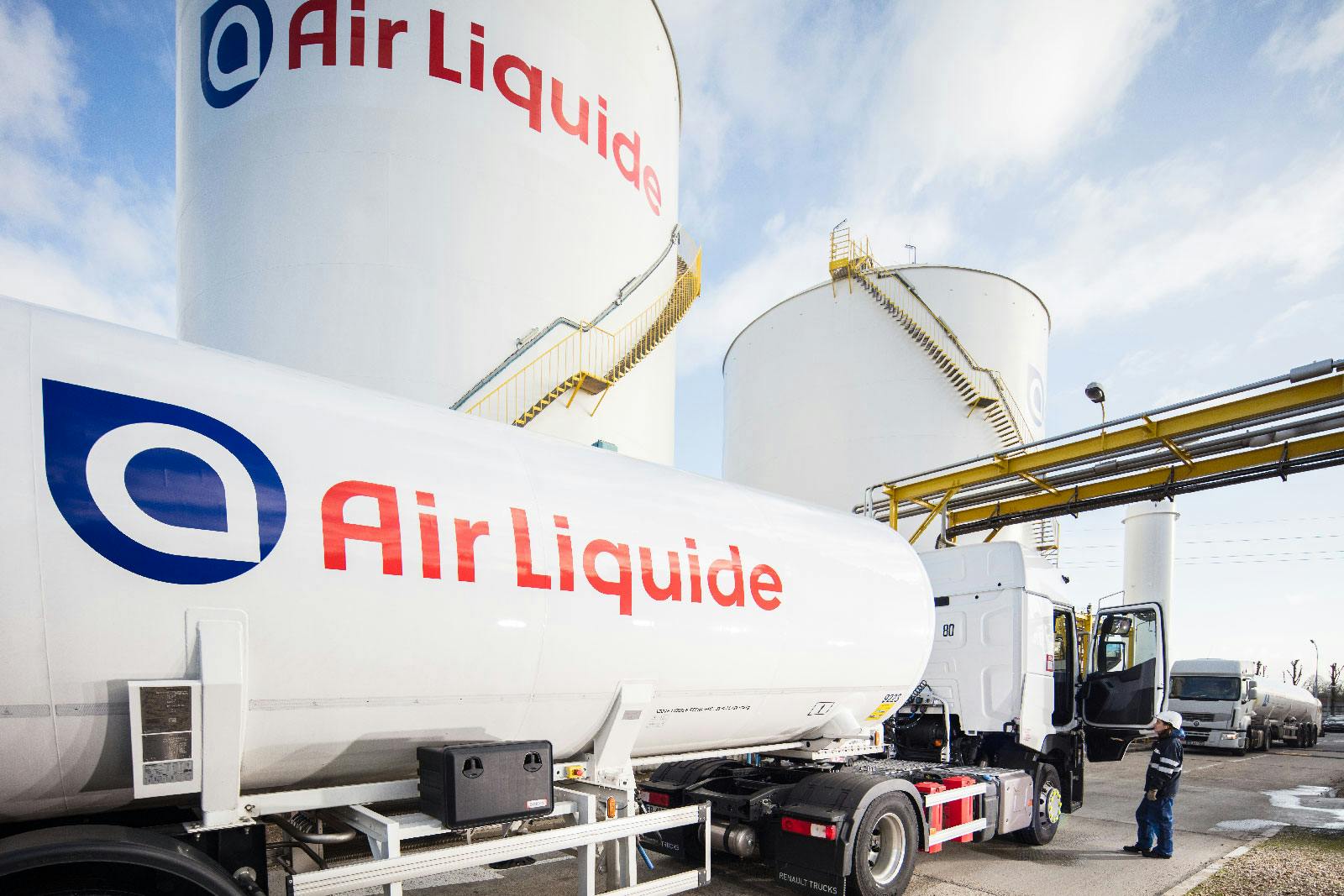
Our solution
- A consolidated view of all shipments in a single platform
- API integration with shipper ERP to pull the latest transport orders and to push the latest ETA
- Real-time containers tracking via shipping lines, AIS and satellite data
- Automatic alerts sent to proactively notify the team about delays and pressure variations